Iron Age in Tamil Nadu - Part 01
(இதன் தமிழ் வடிவத்திற்கு இங்கே சொடுக்கவும்)
Antiquity of Iron in Tamil Nadu
- Shaping History Through Resources: India’s history has been shaped by various cultural and technological advancements.
- Role of Iron Ore in Tamil Nadu: The availability of natural resources, including iron ores, played a significant role in this development, especially in Tamil Nadu.
- Importance of Iron Technology: Iron technology is one of humanity's most important technological innovations.
- Advantages of Iron Tools: Iron tools were cheaper, more durable, and efficient compared to copper and bronze tools.
- Impact on Agriculture and Society: The use of iron tools accelerated agricultural production and contributed to socio-economic development in Tamil Nadu.
- Iron Technology’s Crucial Role: Iron technology played a crucial role in the history of Tamil Nadu due to the abundance of iron ore deposits.
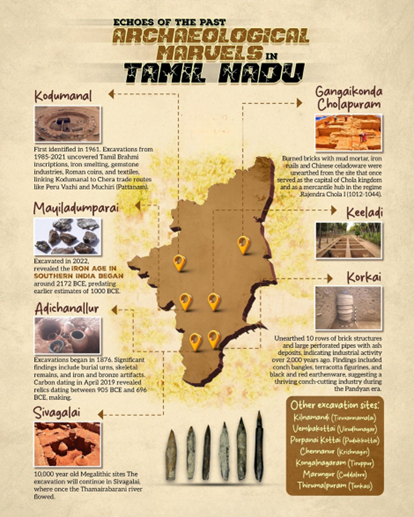
Radiometric Dating and Archaeological Evidence
- Insights from Recent Discoveries: Radiometric dates from Tamil Nadu have provided insights into the ancient use of iron in the region.
- Excavations at Adichanallur: Excavations at Adichanallur revealed a complex interaction between iron and high-tin bronze artifacts, dating back to around the mid-15th century BCE.
- Lack of a Copper Age in Tamil Nadu: Tamil Nadu did not experience a significant Copper Age, unlike northern India.
- Scarcity of Copper Ore: This was primarily due to the lack of sufficient exploitable copper ore in the region.
- Association of Bronze and Iron Tools: High-tin bronze objects were discovered in association with iron tools, suggesting a connection between the two.
- Challenges to Traditional Views: This association challenges the traditional view that copper smelting preceded the introduction of iron.
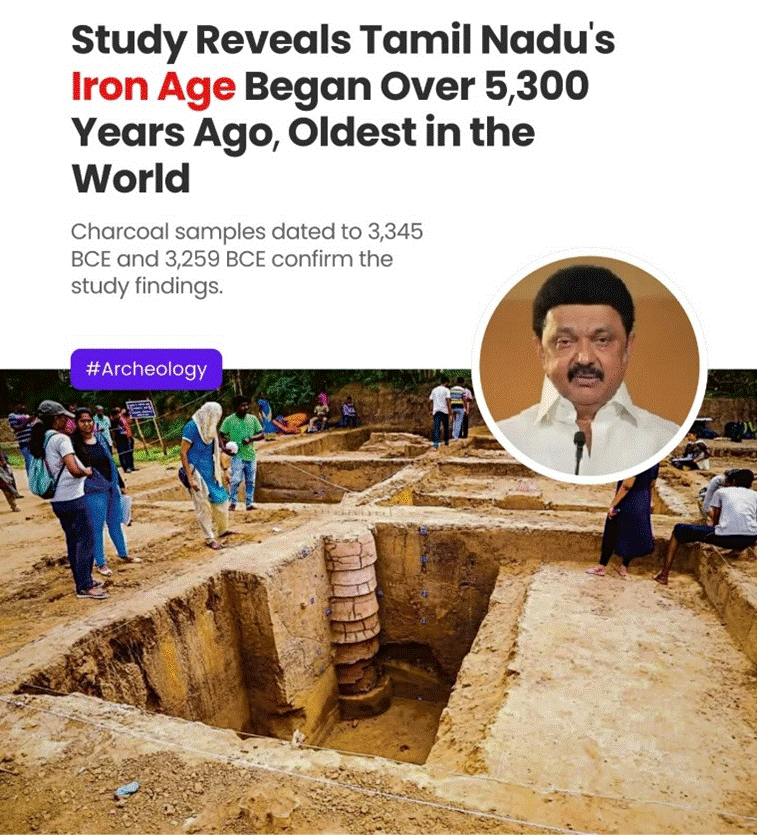
High-Tin Bronze Artifacts in the Iron Age Context
- Bronze and Iron Artifacts Together: High-tin bronze objects were found alongside iron tools at excavation sites like Adichanallur (Thoothukudi district), Sasthapuram (Theni district), and Tirumalapuram (Tirunelveli District).
- Cultural Context of Iron and Bronze: These artifacts suggest that bronze items were part of the same cultural context as iron tools.
- Iron Before Copper: The discovery implies that iron entered Tamil Nadu before copper, contradicting traditional historical perspectives.
- Imported Bronze Objects: Despite the abundance of high-tin bronze objects, no local production centers for these items have been identified in Tamil Nadu.
- External Trade Networks: It is likely that these bronze artifacts were imported from regions outside Tamil Nadu.
- Trade and Cultural Influences: The discovery raises questions about trade networks and external influences during the Iron Age in Tamil Nadu.
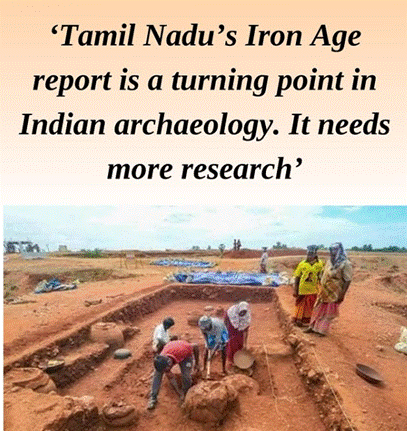
Iron as a Metal
Availability of Iron Ores
- Types of Iron Ores: The availability of suitable iron ores such as hematite, magnetite, limonite, goethite, and laterite containing iron nodules was an important factor for the iron smelting industry.
- Proximity to Sources: The convenient distance of these ores from smelting centers was crucial for the development of ironworking.
Iron Smelting Process
- High Temperature Requirements: Iron smelting required a high temperature of around 1200–1400°C.
- Steps in the Process: The smelting process involved several stages, starting with the preparation of fuel/charcoal, followed by furnace setup, fixing the tuyere, adjusting wind direction, timing the execution, and finally collecting the wrought iron.
- Role of Furnace and Bellows: The furnace and bellows played a critical role in maintaining the necessary high temperature for smelting.
Natural Iron Ores and Metallurgy
- Commonly Occurring Ores: Common natural iron ores include ferric oxide (Fe2O3), magnetite (Fe3O4), and ferric oxy-hydroxide (FeO (OH)).
- Metallurgical Process: These ores undergo a metallurgical process to attain their final form, which is classified based on the carbon content.
Classification of Iron Based on Carbon Content
- Pig Iron: Iron with a carbon content of 3.8–4.7% is known as pig iron.
- Cast Iron: Iron with a carbon content of 2–2.5% is classified as cast iron.
- Wrought Iron: Iron with a low carbon content of 1.5–2% is called wrought iron (low carbon steel).
- Effect of Carbon on Iron: The carbon content in iron determines its rigidity, flexibility, ductility, and toughness.
- Higher carbon content increases rigidity but decreases flexibility, ductility, and toughness.
- Wrought iron, with lower carbon content, was preferred by ancient iron smiths for its malleability.
Reducing Carbon Content
- Process to Reduce Carbon: The most common technique to reduce the carbon percentage in iron is by inducing oxygen gas onto the molten metal.
- Carbon Removal: This results in the release of carbon into the atmosphere as carbon monoxide and carbon dioxide.
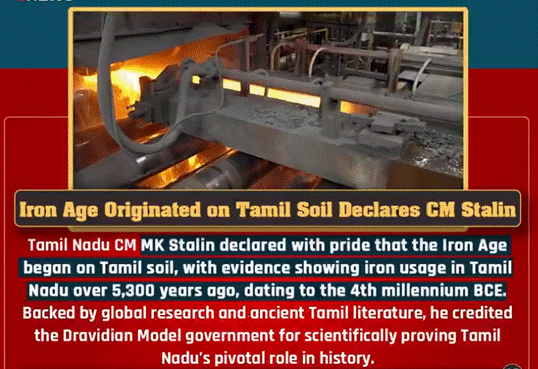
Iron Furnace
Importance of Iron Production in India
- Early Iron Production: India emerged as a major and early center of iron production.
- Geological and Archaeological Evidence: Geological enumeration of iron ores, literary sources, archaeological data, and government reports have highlighted pre-industrial iron-smelting operations across the subcontinent.
- Systematic Studies: Early studies on pre-industrial iron-smelting operations were first conducted by John Percy in 1864.
- Comprehensive Survey: Valentine Ball (1881) conducted the most comprehensive survey of iron ores, smelting methods, and distribution in India, published in the Manual of the Geology of India.
- Detailed Accounts: ’Percy’s Metallurgy: Iron and Steel’ provides the most systematic discussions of pre-industrial iron-smelting processes in India.
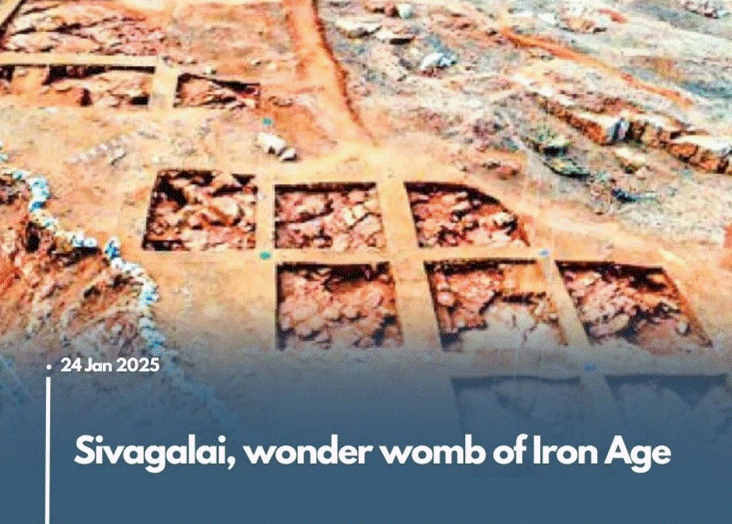
Types of Pre-Industrial Iron Smelting Furnaces
- Types of Furnaces: Percy described three basic types of pre-industrial iron smelting furnaces, with the first two types being found in Tamil Nadu.
- Furnaces in Tamil Nadu: The first two types of furnaces have been encountered in archaeological contexts at sites like Mullur, Perungalur, Vallatirakottai in the Pudukottai region, and Idyapalyam (Thiruvallur District) Chettipalayam and Irugur (Coimbatore district), Kaniyampundi (Tiruppur District), Nichchampalayam and Kodumanal (Erode District) in Tamil Nadu’s magnetite ore-bearing zones.
Description of the First Type of Furnace
- Structure and Size: The first type of furnace was simple and circular in form, with a height varying from 2 to 4 feet.
- Dimensions: The width across the hearth at the bottom ranged from 10 to 15 inches, and at the top, it ranged from 6 to 12 inches.
- Material: The furnace was made entirely of carefully tempered clay.
- The lower part of the furnace wore away quickly and was constantly repaired with fresh clay linings.
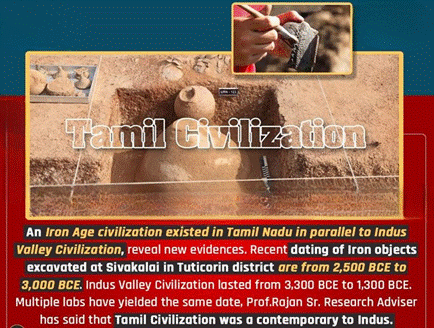
Kodumanal Iron Furnace
Excavation at Kodumanal
- Furnace Description: The furnace excavated at Kodumanal had a circular base with a diameter of 115 cm at a depth of 65 cm, situated directly on the natural soil.
- Furnace Characteristics: The furnace area showed white coloration, possibly due to high temperatures.
- Artifacts Found: Iron slag, burnt clay embedded with slag, tuyere pieces with vitrified mouths, and a granite slab were collected near the furnace.
- Smooth Surface of Slag: Some iron slag stuck to the furnace walls had a smooth surface.
Furnace Temperature and Iron Production
- Temperature of Furnace: The furnace at Kodumanal likely reached a temperature of 1300°C, which is above the minimum required to reduce iron oxides to iron but below the melting point of the metal.
- Semi-Solid Iron: The iron produced was semi-solid, in the form of sponge iron or raw bloom, with slag draining away during the process.
Iron Smelting Location and Cultural Context
- Open Area for Smelting: The absence of postholes and floor levels, and the presence of only potsherds in the smelting area, suggest that iron smelting took place in an open area on the edge of the habitation site.
- Other Sites with Slag Mounds: Large iron slag mounds have been noted at Idyapalayam, Nichchampalayam, and Chettipalayam.
- Cultural Artefacts: The presence of russet-coated ware, black-and-red ware, and graffiti marks at habitation mounds suggests these sites were active as early as the 5th century BCE.
Second Type of Furnace (Cavity Furnace)
- Furnace Description: The second type of furnace, described by Percy, was a cavity made in a clay bank, cylindrical in shape, with a diameter of 15 to 18 inches and a depth of about 2.5 feet.
- Tuyeres: The furnace had two openings at the bottom, with one opening for the tuyere and the other for removing slag.
- The furnace was filled with charcoal, and alternate charges of ore and charcoal were introduced while the bellows operated at full blast.
- Tapping Cinder: As the cinder rose to a certain height, it was tapped with an iron bar.
- The smelted ore was shaped into a ball, then removed with tongs.
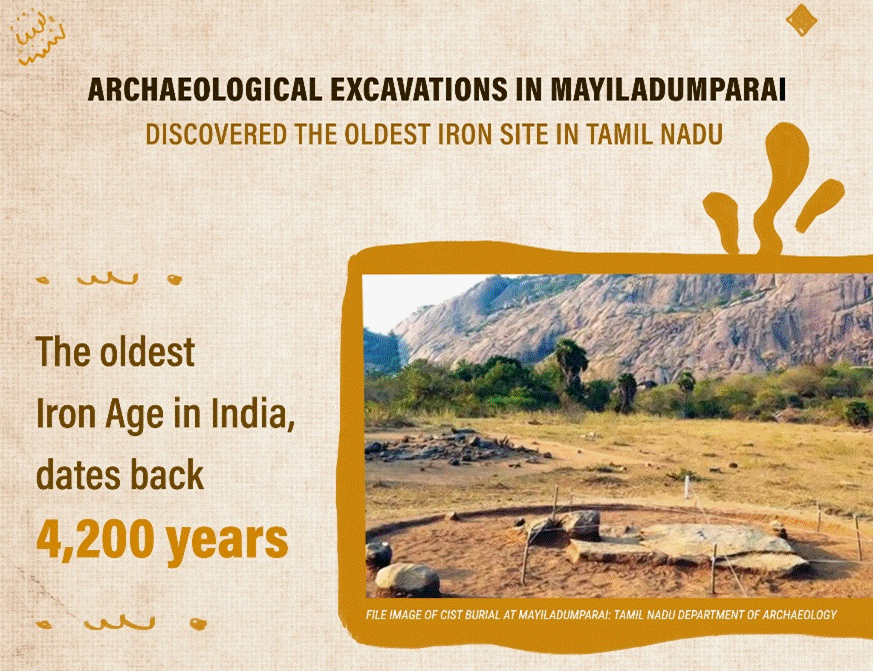
Furnace Efficiency and Improvements
- Furnace Reusability: Unlike the first type of furnace, the lower part of this furnace did not need to be removed for a fresh charge, saving time and improving efficiency.
- Catalan Furnace: Percy referred to this type as a "small Catalan furnace," and similar furnaces were found at Perungalur, Vallatirakottai, and Suruliappan village.
- Location of Furnaces: These furnaces were typically found in lateritic zones, contrasting with the circular and cylindrical furnaces found in magnetite ore-bearing zones.
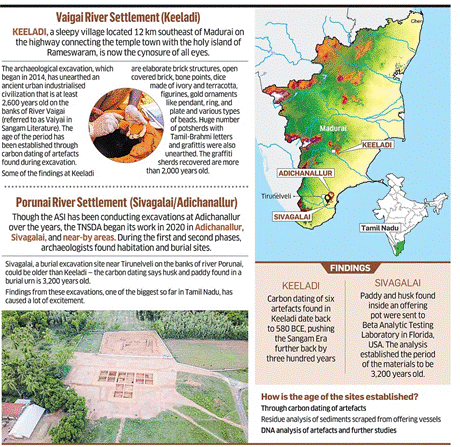
Third Type of Furnace (Vertical Furnace)
- Furnace Description: The third type of furnace was a cavity scooped out in a clay mound, with a height of 8 to 10 feet on the side and 6 to 7 feet inside.
- The internal diameter at the top was 18 inches, and the furnace had a removable front wall.
- Construction Details: The base was made with perforated tiles, with cow dung placed above the base and tuyeres introduced above the dung.
- Smelting Process: The furnace was filled with charcoal, and ore and charcoal were alternately introduced.
- The smelting process lasted 12 to 16 hours, with cinder tapped at intervals.
- Iron and Steel Production: The mass of iron and cinder, weighing 150 to 200 pounds, was cut into pieces.
- This type of furnace produced higher-grade iron and steel, with the proportion of malleable iron and natural steel depending on the ore used.
Absence of Third Type Furnaces in Tamil Nadu
- Lack of Third-Type Furnaces: Such furnaces have not yet been encountered in Tamil Nadu, although there is potential for future exploration to uncover them.
- Other Furnace Materials: Furnace materials were found at sites like Ariyanipatti and Venkatanaickampatti (Pudukottai district), suggesting that similar furnaces might have been used in these regions.
-------------------------------------